














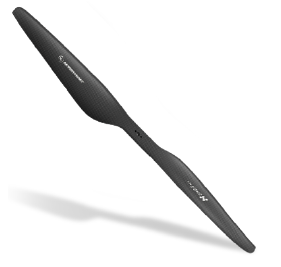











Product Name |
|
|||||||||||||||||||||||||||||||||||||||||||||||||||||||||
Specifications |
|
The purpose of this website is only to introduce you to the basic situation of HOBBYWING company and product information. Unless otherwise stated, all information provided on this website should not be regarded as an offer or acceptance, and this website will not assume any binding obligations to you as a result of the provision of information. For all your requests, HOBBYWING reserves the full right to decide whether to commit or not.
This Website and its contents are provided for your convenience on an "as is" basis and your use of this Website is at your sole risk. HOBBYWING does not guarantee that this website will be uninterrupted or error-free, and reserves the right to amend this website or withdraw access to this Website at any time. We make no warranties, express or implied, as to the content, existence, accuracy or reliability of this Website, including, but not limited to, warranties of title, non-infringement or implied warranties of merchantability or fitness for a particular purpose or use.
HOBBYWING shall not be liable for any direct, indirect, incidental, special or consequential damages, loss of profits or business interruption caused by the use or inability to use the services provided by the Website, even if HOBBYWING has been advised of the possibility of similar losses. The exclusions and limitations of the warranty liability of HOBBYWING shall be effective to the extent permitted by applicable law.
HOBBYWING shall not be liable for any damage or loss to your computer system or any other software, hardware, IT system or property caused by viruses or other destructive programs caused by accessing, viewing and using this website or downloading any content from this Website (including but not limited to 2D model files, 3D model files).
HOBBYWING shall not be liable for any direct or indirect damage or loss caused by any third party using illegal means to access the website to obtain the relevant passwords, information and content.
If you or your company is located in the United States or Canada, you need to fill out this disclaimer confirmation letter online and submit it successfully before you can download the relevant materials you are interested in. The link address you fill in online is https://www.hobbywingdirect.com/pages/digital-file-release-form
If you do not agree with this disclaimer, please do not continue to this page. If you continue to access, browse and use this interface, you have read, understood and agreed to be bound by this statement and comply with all applicable laws and regulations.
HOBBYWING reserves the right to correct, modify and update this statement at any time.
Product Name |
|
|||||||||||||||||||||||||||||||||||||||||||||||||||||||||
Specifications |
|
The purpose of this website is only to introduce you to the basic situation of HOBBYWING company and product information. Unless otherwise stated, all information provided on this website should not be regarded as an offer or acceptance, and this website will not assume any binding obligations to you as a result of the provision of information. For all your requests, HOBBYWING reserves the full right to decide whether to commit or not.
This Website and its contents are provided for your convenience on an "as is" basis and your use of this Website is at your sole risk. HOBBYWING does not guarantee that this website will be uninterrupted or error-free, and reserves the right to amend this website or withdraw access to this Website at any time. We make no warranties, express or implied, as to the content, existence, accuracy or reliability of this Website, including, but not limited to, warranties of title, non-infringement or implied warranties of merchantability or fitness for a particular purpose or use.
HOBBYWING shall not be liable for any direct, indirect, incidental, special or consequential damages, loss of profits or business interruption caused by the use or inability to use the services provided by the Website, even if HOBBYWING has been advised of the possibility of similar losses. The exclusions and limitations of the warranty liability of HOBBYWING shall be effective to the extent permitted by applicable law.
HOBBYWING shall not be liable for any damage or loss to your computer system or any other software, hardware, IT system or property caused by viruses or other destructive programs caused by accessing, viewing and using this website or downloading any content from this Website (including but not limited to 2D model files, 3D model files).
HOBBYWING shall not be liable for any direct or indirect damage or loss caused by any third party using illegal means to access the website to obtain the relevant passwords, information and content.
If you or your company is located in the United States or Canada, you need to fill out this disclaimer confirmation letter online and submit it successfully before you can download the relevant materials you are interested in. The link address you fill in online is https://www.hobbywingdirect.com/pages/digital-file-release-form
If you do not agree with this disclaimer, please do not continue to this page. If you continue to access, browse and use this interface, you have read, understood and agreed to be bound by this statement and comply with all applicable laws and regulations.
HOBBYWING reserves the right to correct, modify and update this statement at any time.