













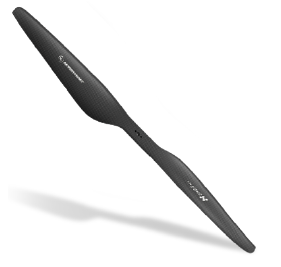











Sine Wave-driven (FOC) ESC
The revolutionary sine wave-driven technology will make the ESC generate some braking effect, recycle the energy when
the motor slows down and have smoother throttle linearity. Compared to BLDC square wave-driven ESCs, the FOC ESC
monitors the current and is driven by current control while BLDC ESCs monitor the voltage and are driven by voltage
control. The ESC, which adopted the FOC driving technology, for agricultural applications has the following advantages:
1. Lower sound. No annoying noise.
2. Lower temperature. The temperature can be 10℃ lower than the one of BLDC-driven ESCs.
3. Higher efficiency. The overall efficiency can be increased by 8% to 10% than the one of BLDC-driven ESCs.
4. Rapider response. More stable flight and quicker response.
Sine Wave-driven (FOC) ESC
Special Motor for
Agricultural Applications
XRotor PRO 6215 180KV
Special ESC for
Agricultural Applications
XRotor PRO 80A HV FOC V4
Special Propeller for
Agricultural Applications
XRotor PRO 2388
Waterproof, Rustproof & Anti-corrosive
The ESC which features the injection-molded waterproof heatsink housing
and the motor consists of the imported waterproof NSK bearings, shaft with
patented waterproof structure, anti-corrosive windings (went through
vacuum dip coating treatment for twice), stator core (went through
electroplating rustproof and anti-corrosive treatment), and rotor magnet steel
(went through nickel-copper-nickel electroplating rustproof and
anti-corrosive treatment) make the combo waterproof to IPX7 standard.
All the protective design effectively guarantees the excellent waterproof,
rustproof and anti-corrosive feature of the power system combo.
Waterproof, Rustproof
& Anti-corrosive
Special ESC for
Agricultural Applications
XRotor PRO 80A HV FOC V4
Special Motor for
Agricultural Applications
XRotor PRO 6215 180KV
Special Propeller for
Agricultural Applications
XRotor PRO 2388
Data-logging &
Multiple Protections
The ESC outputs "black box" data to monitor the power
system's operation, record trajectories, discover potential
issues and activate corresponding protections in real time for
helping flight controller control the system effectively. Multiple
protection functions like power-on self test (for detecting
internal faults), voltage, current and motor lock-up perfectly
protect the system from all the possible risks.
(Note: Output data contains input throttle, output throttle,
RPM, input voltage, input current, output current,
capacitor temperature, MOSFET temperature and etc.)
Data-logging &
Multiple Protections
Data-logging & Multiple Protections
Power-on
Self Test
Start-up Voltage
Protection
Overcurrent
Protection
Motor Lock-up
Protection
Light & Compact Design
The compact and light design makes the ESC more
applicable to heavy-duty drones (with over 4 rotors),
the reserved threaded holes and slots on the heatsink
housing simplify and diversify the installation.
Light & Compact Design
Optimized FOC Power System
When pairing with the balanced motor (went through the sine-wave EMF optimization)
and propeller, the ESC adopted the latest FOC sine wave-driven algorithm will
generate (30%) less heat, have rapider response, and make the drone more stable
than traditional sine wave-driven ESCs. The FOC solution greatly improves the
battery's sustainability, increases the flight time and effectively protects the motor and
battery and prolongs their service lives via current control.
Optimized FOC
Power System
The ESC features the latest FOC
sine wave-driven algorithm
Low Vibration & Noise
The precisely balanced rotor guarantees users low vibration
and noise during the motor's high-speed rotation.
Low Vibration & Noise
High-efficiency Heat Dissipation Structure
Besides the layered structure design, heat-conductive copper bars
and heatsink are fitted together to quickly transfer all internal heat to
the integrated heatsink housing of the ESC. The centrifugal fan
design adopted by the motor rotor can autonomously dissipate
heat in operation. All this will effectively improve the flight
performance of the drone.
High-efficiency Heat
Dissipation Structure
Special Motor for Agricultural Applications
XRotor PRO 6215 180KV
Special Heat-resistant Windings
Heat-resistant Magnets
Triple Interlocking Design
The HOBBYWING patented interlocking structure design (that’s the
circlip or snap ring, lock sleeve, and screw) implemented by the
motor rotor guarantees the great stability and reliability of the motor.
Triple Interlocking Design
Lock Sleeve
Circlip
Screw
Strong Impetus
The 23-inch precisely molded propeller which is made
of some light and solid composite material has great
strength, stiffness and excellent shape (which guarantees
the minimum air friction in operation). It's impact-resistant,
anti-abrasive, collapsible (with blades are replaceable)
and can produce the thrust of up to 12kg when combining
with the optimized motor's electromagnetic design and the
high-efficiency ESC's FOC algorithm.
Strong Impetus
Impact-resistant & Heat-resistant
The alloy shaft combined with overall reinforced CNC-machined rotor guarantees
the high impact resistance, the special heat-resistant windings combined with
heat-resistant magnets guarantees the powerful and continuous overload
capability, and the wear-proof rubber sleeve which is designed to protect and fix
the motor wires guarantees the durability & reliability of the motor.
Impact-resistant
& Heat-resistant
Special Heat-resistant Windings
Heat-resistant Magnets
Regular Firmware Updates
Free of Charge
You can upgrade the ESC with the Hobbywing USB LINK
software, a LCD program box (item sold separately) and a
laptop. Hobbywing updates its ESC firmware regularly
giving you upgraded features more often when available.
Regular Firmware Updates
Free of Charge
Voltage(V) |
Propeller |
Throttle(%) |
Trust(g) |
Ampere(A) |
Power(W) |
Efficiency(g/W) |
48V(12S LiPo) |
23 Inch |
41% |
2019 |
3.5 |
172.5 |
11.7 |
49% |
2995 |
6.6 |
320.5 |
9.3 |
||
56% |
4017 |
9.7 |
485.2 |
8.3 |
||
62% |
5016 |
13.8 |
676.1 |
7.4 |
||
67% |
5999 |
17.9 |
873.0 |
6.9 |
||
73% |
7007 |
22.8 |
1112.5 |
6.3 |
||
79% |
7989 |
28.1 |
1372.8 |
5.8 |
||
84% |
9003 |
33.7 |
1644.6 |
5.5 |
||
89% |
9996 |
39.8 |
1942.1 |
5.1 |
||
94% |
11014 |
47.1 |
2295.5 |
4.8 |
||
100% |
12033 |
55.1 |
2678.5 |
4.5 |
Product Name | |
Specifications | Max. Thrust Recommended Takeoff Weight Recommended LiPo Battery Operating Temperature Combo Weight (approx.) Waterproof Rating |
Motor | Model KV Rating Outer Diameter Weight Mounting Holes for Propeller Mounting Holes for Motor Holder Output Wires |
ESC | Model Recommended Input Voltage Max. Input Voltage Max. Input Current BEC Input Wires Output Wires Weight Operating Pulse Width Throttle Signal Frequency Size |
Propeller | Model Weight |
Product Name | XRotor6 Series Power Combo for Agriculutral Drones | |
Specifications | Max. Thrust Recommended Takeoff Weight Recommended LiPo Battery Operating Temperature Combo Weight (approx.) Waterproof Rating |
12kg/Axis(48V) 3.5kg-5kg/Axis 12S -20~65℃ 502.5g IPX7 |
Motor | Model KV Rating Outer Diameter Weight Mounting Holes for Propeller Mounting Holes for Motor Holder Output Wires |
XRotor PRO 6215 180KV 180 69mm 345g M3 M4 HW High-Strand-Count, Glassfiber-Insulated Wire with 4mm Bullet Connectors |
ESC | Model Recommended Input Voltage Max. Input Voltage Max. Input Current BEC Input Wires Output Wires Weight Operating Pulse Width Throttle Signal Frequency Size |
XRotor PRO 80A HV FOC V4 12S LiPo 52.2V 80A(With Heat Dissipation) NO 12AWG 14AWG 82.5g(w/o Wires) 1100us-1940us 50-500Hz 83.5x35x19.4mm |
Propeller | Model Weight |
XRotor PRO 2388 75g |
Sine Wave-driven (FOC) ESC
The revolutionary sine wave-driven technology will make the ESC generate some braking effect, recycle the energy when the motor slows down and have smoother throttle linearity. Compared to BLDC square wave-driven ESCs, the FOC ESC monitors the current and is driven by current control while BLDC ESCs monitor the voltage and are driven by voltage control. The ESC, which adopted the FOC driving technology, for agricultural applications has the following advantages: 1. Lower sound. No annoying noise. 2. Lower temperature. The temperature can be 10℃ lower than the one of BLDC-driven ESCs. 3. Higher efficiency. The overall efficiency can be increased by 8% to 10% than the one of BLDC-driven ESCs. 4. Rapider response. More stable flight and quicker response.
Sine Wave-driven (FOC) ESC
Waterproof, Rustproof & Anti-corrosive
The ESC which features the injection-molded waterproof heatsink housing and the motor consists of the imported waterproof NSK bearings, shaft with patented waterproof structure, anti-corrosive windings (went through vacuum dip coating treatment for twice), stator core (went through electroplating rustproof and anti-corrosive treatment), and rotor magnet steel (went through nickel-copper-nickel electroplating rustproof and anti-corrosive treatment) make the combo waterproof to IPX7 standard. All the protective design effectively guarantees the excellent waterproof, rustproof and anti-corrosive feature of the power system combo.
Waterproof, Rustproof
& Anti-corrosive
Data-logging & Multiple Protections
The ESC outputs "black box" data to monitor the power system's operation, record trajectories, discover potential issues and activate corresponding protections in real time for helping flight controller control the system effectively. Multiple protection functions like power-on self test (for detecting internal faults), voltage, current and motor lock-up perfectly protect the system from all the possible risks. (Note: Output data contains input throttle, output throttle, RPM, input voltage, input current, output current, capacitor temperature, MOSFET temperature and etc.)
Data-logging &
Multiple Protections
Light & Compact Design
The compact and light design makes the ESC more applicable to heavy-duty drones (with over 4 rotors), the reserved threaded holes and slots on the heatsink housing simplify and diversify the installation.
Light & Compact Design
Optimized FOC Power System
When pairing with the balanced motor (went through the sine-wave EMF optimization) and propeller, the ESC adopted the latest FOC sine wave-driven algorithm will generate (30%) less heat, have rapider response, and make the drone more stable than traditional sine wave-driven ESCs. The FOC solution greatly improves the battery's sustainability, increases the flight time and effectively protects the motor and battery and prolongs their service lives via current control.
Optimized FOC
Power System
Low Vibration & Noise
The precisely balanced rotor guarantees users low vibration and noise during the motor's high-speed rotation.
Low Vibration & Noise
High-efficiency Heat Dissipation Structure
Besides the layered structure design, heat-conductive copper bars and heatsink are fitted together to quickly transfer all internal heat to the integrated heatsink housing of the ESC. The centrifugal fan design adopted by the motor rotor can autonomously dissipate heat in operation. All this will effectively improve the flight performance of the drone.
High-efficiency Heat
Dissipation Structure
Triple Interlocking Design
The HOBBYWING patented interlocking structure design (that’s the circlip or snap ring, lock sleeve, and screw) implemented by the motor rotor guarantees the great stability and reliability of the motor.
Triple Interlocking Design
Strong Impetus
The 23-inch precisely molded propeller which is made of some light and solid composite material has great strength, stiffness and excellent shape (which guarantees the minimum air friction in operation). It's impact-resistant, anti-abrasive, collapsible (with blades are replaceable) and can produce the thrust of up to 12kg when combining with the optimized motor's electromagnetic design and the high-efficiency ESC's FOC algorithm.
Strong Impetus
Impact-resistant & Heat-resistant
The alloy shaft combined with overall reinforced CNC-machined rotor guarantees the high impact resistance, the special heat-resistant windings combined with heat-resistant magnets guarantees the powerful and continuous overload capability, and the wear-proof rubber sleeve which is designed to protect and fix the motor wires guarantees the durability & reliability of the motor.
Impact-resistant
& Heat-resistant
Regular Firmware Updates Free of Charge
You can upgrade the ESC with the Hobbywing USB LINK software, a LCD program box (item sold separately) and a laptop. Hobbywing updates its ESC firmware regularly giving you upgraded features more often when available.
RRegular Firmware Updates
Free of Charge
Voltage(V) |
Propeller |
Throttle(%) |
Trust(g) |
Ampere(A) |
Power(W) |
Efficiency(g/W) |
48V(12S LiPo) |
23 Inch |
41% |
2019 |
3.5 |
172.5 |
11.7 |
49% |
2995 |
6.6 |
320.5 |
9.3 |
||
56% |
4017 |
9.7 |
485.2 |
8.3 |
||
62% |
5016 |
13.8 |
676.1 |
7.4 |
||
67% |
5999 |
17.9 |
873.0 |
6.9 |
||
73% |
7007 |
22.8 |
1112.5 |
6.3 |
||
79% |
7989 |
28.1 |
1372.8 |
5.8 |
||
84% |
9003 |
33.7 |
1644.6 |
5.5 |
||
89% |
9996 |
39.8 |
1942.1 |
5.1 |
||
94% |
11014 |
47.1 |
2295.5 |
4.8 |
||
100% |
12033 |
55.1 |
2678.5 |
4.5 |
Product Name | XRotor6 Series Power Combo for Agriculutral Drones | |
Specifications | Max. Thrust Recommended Takeoff Weight Recommended LiPo Battery Operating Temperature Combo Weight (approx.) Waterproof Rating |
12kg/Axis(48V) 3.5kg-5kg/Axis 12S -20~65℃ 502.5g IPX7 |
Motor | Model KV Rating Outer Diameter Weight Mounting Holes for Propeller Mounting Holes for Motor Holder Output Wires |
XRotor PRO 6215 180KV 180 69mm 345g M3 M4 HW High-Strand-Count, Glassfiber-Insulated Wire with 4mm Bullet Connectors |
ESC | Model Recommended Input Voltage Max. Input Voltage Max. Input Current BEC Input Wires Output Wires Weight Operating Pulse Width Throttle Signal Frequency Size |
XRotor PRO 80A HV FOC V4 12S LiPo 52.2V 80A(With Heat Dissipation) NO 12AWG 14AWG 82.5g(w/o Wires) 1100us-1940us 50-500Hz 83.5x35x19.4mm |
Propeller | Model Weight |
XRotor PRO 2388 75g |
Product Name | XRotor6 Series Power Combo for Agriculutral Drones | |
Specifications | Max. Thrust Recommended Takeoff Weight Recommended LiPo Battery Operating Temperature Combo Weight (approx.) Waterproof Rating |
12kg/Axis(48V) 3.5kg-5kg/Axis 12S -20~65℃ 502.5g IPX7 |
Motor | Model KV Rating Outer Diameter Weight Mounting Holes for Propeller Mounting Holes for Motor Holder Output Wires |
XRotor PRO 6215 180KV 180 69mm 345g M3 M4 HW High-Strand-Count, Glassfiber-Insulated Wire with 4mm Bullet Connectors |
ESC | Model Recommended Input Voltage Max. Input Voltage Max. Input Current BEC Input Wires Output Wires Weight Operating Pulse Width Throttle Signal Frequency Size |
XRotor PRO 80A HV FOC V4 12S LiPo 52.2V 80A(With Heat Dissipation) NO 12AWG 14AWG 82.5g(w/o Wires) 1100us-1940us 50-500Hz 83.5x35x19.4mm |
Propeller | Model Weight |
XRotor PRO 2388 75g |