-
Industry-level motor technologyhas higher specifications and requires high grade
raw materials, better tolerances, to provide
reliability and performance. -
Brand new exterior design,optimized fan ports effectively
improve the protection level. -
The new magnetic circuit
design optimizes the
anti-emotive force harmonics,that produce a higher sine wave and is better
matched with the ESC.
-
The recommended thrust is3kg+
-
The efficiency is11g/w+
-
Long flight time
thrust is



-
(12S 36Ah)
-
The takeoff weight<10kg
-
The endurance120minutes
New Technology
Extremely Lightweight
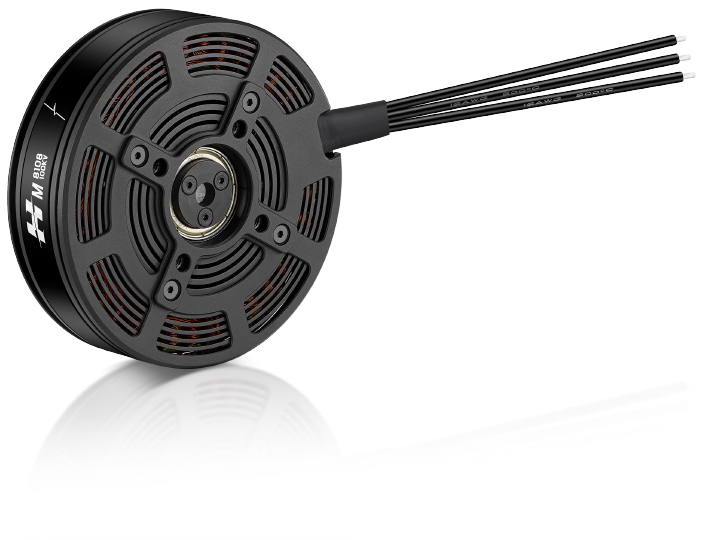
Quality Materials,
Safe and Reliable
reliable guarantee for motor performance.
-
High-quality bearingsand low friction torque effectively
extend the lifespan of the motor. -
High-strength aviation aluminum7075-T651
-
precisionCNC
machined rotor bracket -
The outer rotor casing is made of20# seamless steel rotor with nickel
electrophoresis design, which has excellent magnetic conductivity
and corrosion resistance. -
16AWGhighly flexible silicone wire,
low resistivity and good toughness -
High-performance iron core punched from0.2mmlow-loss silicon steel sheet
Combinations
- Motor
M 8108 HP
Battery
12S LiPo - Propeller
GP28×9.2"/GP29×9.5"/ML30*9.8"
Thrust/rotor
2.5~3.5kg - ESC
XRotor Pro-H60A-14S
Takeoff weight of quadrotor
10.0~14.0kg
- Motor
M 8110 HP
Battery
12S LiPo - Propeller
GP29×9.5"/ML30*9.8"/GP32×10.5"
Thrust/rotor
3.0~4.0kg - ESC
XRotor Pro-H60A-14S
Takeoff weight of quadrotor
12.0~16.0kg